Stocktaking, Supply Chain
and Merchandising
Working together with you as one team
At RGIS, we deliver expert outsourced stocktaking, supply chain audits, asset management and merchandising services
across a multitude of sectors, including retail, industrial, automotive, aerospace and healthcare.
Sector Solutions
Retail
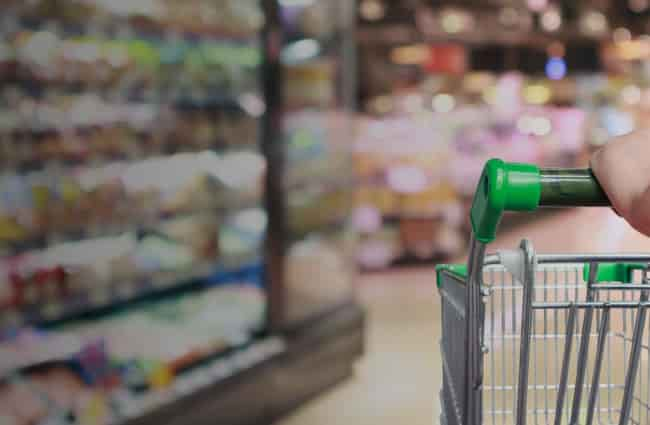
Stocktaking solutions for all types of retail stores, from global chain stores to the local supermarket. RGIS is the partner you can trust for stocktake accuracy, merchandising, store support, store compliance, store insights, store development and store planning.
Industrial
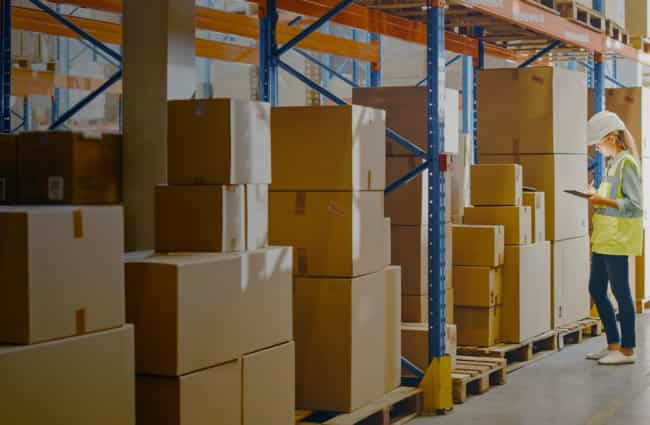
Supply chain solutions for industrial and manufacturing environments. RGIS turn stocktaking problems into manageable solutions with warehouse wall-to-wall counts, pick accuracy, delivery checks and supply chain audits.
Healthcare
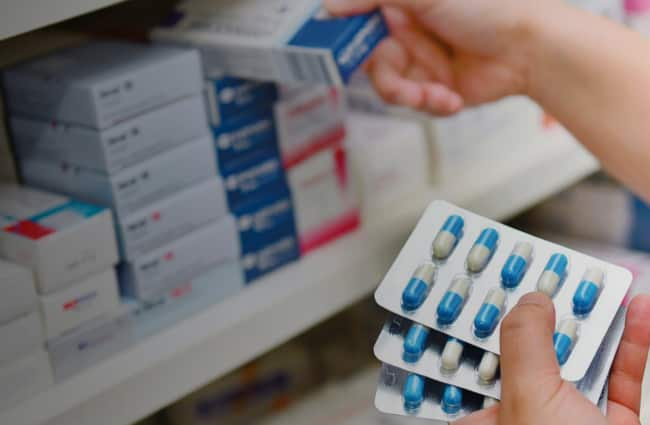
Inventory solutions for integrated healthcare networks to closed door pharmacies. Our fully trained experienced team deliver stocktaking, consignment check and asset management accuracy with surgical precision.
Latest Developments
Case Studies
Join the Team
Careers
RGIS is Hiring...
Stocktaking Associate
Multiple Australia Locations
Merchandising Associate
Multiple Australia Locations
Stocktaking Professional
Multiple Australia Locations
Latest News and Events
RGIS is around the Corner and Around the World
More than
3,500
Global customers
160,000
Over
Stocktakes per year
Servicing
53
Countries worldwide